Canister Performance Requirements of US EPA Method TO-15A
Canister Performance Requirements of US EPA Method TO-15A
By Dan Cardin
Welcome to the first in a series of articles covering the latest US EPA Method TO-15A revision for canister monitoring of VOCs in air. Method TO-15A represents a substantial improvement in canister monitoring methodology, deriving input from the last 20 years of field sampling and laboratory analysis since the prior revision was published in 1999. The TO-15A method is very clearly written and focuses on enhancing performance criteria to improve the certainty in air monitoring results, especially for lower level analysis (ambient air, vapor intrusion/indoor air). This first article highlights important considerations for the new requirements placed on sampling canisters, including both the lower allowable background levels of 0.02 PPBv, as well as the new requirement to validate target compound recovery from each sampling canister used. Also discussed are Entech’s solutions to help laboratories demonstrate compliance with the newly established QA requirements.
Although this article relays the requirements found in US EPA Method TO-15A, the rationale, theory, or background presented for these requirements expressed herein are based on the authors 30+ years of working with hundreds of canister laboratories world-wide, and through the inhouse research conducted at Entech Instruments, and are not necessarily found in the method and in no way represent an endorsement by the EPA. This article provides insight from a company specializing in canister sampling and analysis to help others who are endeavoring to achieve optimal performance of their methods and techniques.
0.02 PPB Allowable Background Levels – New Canister Validation & Ongoing 3 Year Recertification
The EPA has established both initial and on-going requirements for blank testing of canisters used to perform TO-15A. Section 9.4.2 describes the requirement to perform background (blank) testing of canisters once every 3 years that is more rigorous than the ongoing blank testing performed prior to sampling events. New canisters must be taken through this process before use, and older canisters must be tested “As Soon As Possible”. The holding time for this more rigorous background test is the typical holding time for a given laboratory, which is often 30 days, but for some labs only 2 weeks. No mention is made in the method about reducing this test period to just 1 week, but faster and more reliable analytical systems that can process canisters within a shorter period may allow labs to use shorter testing periods, if they can truly hold to these faster sample throughput times.
There are a couple of good reasons why the EPA is likely interested in performing critical testing of both new canisters and thereafter used canisters every 3 years. For new canisters, the potential for contamination may be higher right after manufacturing. In fact, this may be especially problematic with canisters that are only electropolished rather than silica coated. Electropolished canisters are typically not heated to high temperatures during the manufacturing process, potentially leaving oils trapped in the surface during the canister half shell stamping process that may never be properly removed. In contrast, the deposition of a silica coating is done at very high temperatures (>300 deg C) and under a strong vacuum, leaving very little chance for any contamination within the metal surface that could later evolve during storage at ambient temperatures. In addition, silica coatings can permanently encase contaminants that may remain within the metal so that they do not create a volatile background inside of the canister later on.
For canisters already in service, a more rigorous test is performed every 3 years as the EPA wants to verify that “something” has not happened to that canister to change its potential for background formation. Obviously, as canisters are routinely shipped to 3rd parties to perform sampling, there is a chance for exposure to chemical concentrations higher than what is typical in ambient air or to other unexpected chemicals or agents. Along with incidents of high exposure, the wear and tear that commonly occurs while canisters are in service; denting, water and particulate ingestion, prolonged storage with condensed water, to name a few, may alter the canister surface composition potentially causing it to aggressively retain target compounds, or absorb other compounds that decompose over time to create new populations of target compounds. Some of these changes may be dependent on the kind of passivation used on the internal surface. For example, electropolished, “uncoated” canisters may undergo surface oxidation over time that allows greater exposure to the 67% Iron found in 316 stainless steel, resulting in both greater surface area and more aggressive surface adsorption, consequently making the canisters harder to clean. Conversely, the slow surface oxidation of silica coated canisters has been shown to improve the inertness and cleanability of Silonite coated canisters, allowing them to have longer usable lifetimes. Not only have Entech Silonite coated canisters been shown to improve with time, but they can be also be “RENEWED” if exposed to harsh chemicals or large amounts of particulates.
Although the new requirements seem extremely challenging, they are in fact a great addition to the method to ensure low level data accuracy. For initial validation, canisters must be cleaned, filled with zero air at 40-50% relative humidity, and then tested at 24 hours AND at 30 days to verify that background levels are less than 0.02 PPBv. The use of Zero Air as opposed to UHP N2 is now a requirement to ensure that the presence of oxygen in the canister is not contributing in some way to the formation of target compounds, potentially through oxidation of heavier SVOCs on or in the canister surface. The purpose for performing an analysis of the canister after 24 hours is undoubtedly to save the laboratory the additional 29 days of waiting, because if the canister fails at 1 day it will almost certainly fail at 30 days. If a lab specifies a maximum holding time of 2 weeks, then the 30-day period can be reduced to 2 weeks. HOWEVER, care must be taken then in allowing canisters to remain under vacuum too long before sending them out into the field, otherwise that time under vacuum must also be considered in the total time that compounds can outgas from the canister walls.
Finally, since canisters are typically filled without the use of a pump, the EPA has decided that testing for background must be conducted on a recovery basis relative to atmospheric pressure to verify that target compounds are below 0.02PPBv. If a laboratory wants to fill canisters to a positive pressure, say 2 atmospheres absolute (about 14.7 psig ), then the allowable target compound levels must be below 0.01 PPB (0.02/2 ATM). If at 29.4 psig, then compounds must be below 0.02/3 = 0.007 PPBv. One can see that if there is a small amount of background in the analytical system itself, it would be better to fill canisters to just atmospheric pressure to allow a full 0.02PPB of background per target compound in the analysis. If compounds are above 0.02 PPB, the lab can still use these canisters, but they must designate which compounds are not in full compliance with the method. Some compounds that are ubiquitous like Isopropyl Alcohol and Acetone, may frequently be over 0.02 PPB, both in the canisters and in the analytical system, but that is often to be expected.
0.02 PPB Allowable Background Levels – Prior to Sampling
The requirements prior to routine sampling are not as strict. After cleaning, canisters are still filled with Zero Air at 40-50% RH to atmospheric pressure (or 2 atm, with a max 0.01 PPBv background), but testing can be done after 24 hours, and only 1 out of 8 canisters need to be tested. If cleaning 9-16 canisters, then 2 canisters must be tested. If 17-24 canisters in a batch, then 3 canisters must be tested. For any group of 8, if the canister tested does not pass the cleanliness requirements, then another 2 cans from that batch must be tested, and both must pass for the rest of that batch to be acceptable. However, the failed canister must be recleaned in a new batch of 8 canisters. Generally, the canister with the highest sample concentrations should be the one tested for each batch of 8 canisters. TO-15A recognizes that many programs will require the blank testing of every canister, not just 1 in 8.
Recovery Testing
Canisters must now be recovery tested for all target compounds being reported. The standard list for TO-15A is found in the 3 standard cylinders that Entech calls our “TO14 + TO15-Subset + TO15-Plus” standards, except for Ethylene Oxide, which will soon be added to one of these 3 mixes. The challenge concentration cannot be at PPB levels, but rather at more realistic sub-PPB levels of 100-500 ppt. As with the initial blank testing, the EPA suggests testing at 24 hours and at 30 days (2 weeks if labs reduce their allowable holding times), to avoid wasting the additional holding time if the canister does not pass after 1 day. If the canisters do not pass after the first day, it may be due to the standard being improperly delivered to the canister, so the canister should be recleaned, and then a second attempt made at filling the canister with the 100-500 ppt standard. For recovery testing, UHP N2 or Zero Air at 40-50% RH are both acceptable. During the holding period, a recovery of +-30% must be maintained for each compound. Recovery testing must be performed “As Soon As Possible” for untested canisters, new or used, and then once every 3 years.
These are the main canister QA requirements for the new TO-15A method. This does not include the leak check procedure, which will be covered in an upcoming review article. Obviously, if labs can increase their laboratory throughput and subsequently reduce their holding times, they can reduce the time their canisters are out of circulation by using the 2 week option rather than the full 30 days for both blank and recovery testing. Improved accuracy and speed of analysis has been a focus at Entech, and our new FAST 7200A and cryogen-less 7200CTS preconcentrators both demonstrate reduced “injection to injection” cycle times relative to prior Entech models, or other commercially available solutions. The ability to support 1-3 autosamplers simultaneously also improves laboratory throughput, as do the Entech robotic autosamplers, allowing our users to maximize processing speeds while optimizing their analytical results.
Our next article will cover new canister leak check requirements of EPA Method TO-15A, which now must be performed without the external valve cap attached. Remember to turn to Entech for your TO-15A needs. We understand canister sampling and analysis. It’s who we are, it’s what we do.
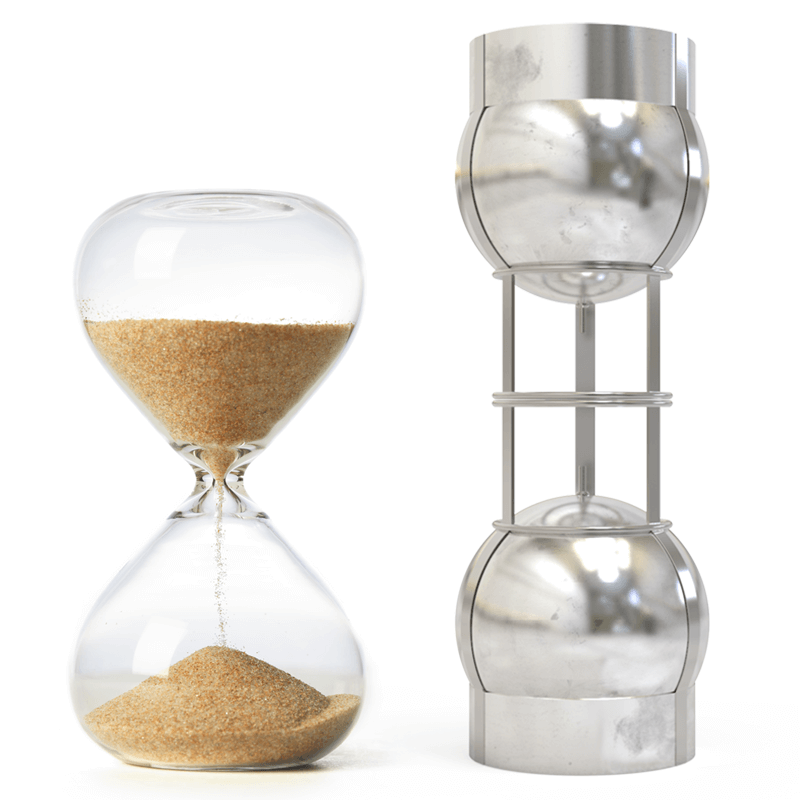
Uncoated canisters don’t save money over the life of the can.
Uncoated cans can oxidize over time and metal oxides, especially iron oxides, cause catalytic losses. When you consider the effective life of uncoated canisters, which can be much shorter than their coated counterparts (especially for those uncoated cans being utilized in high humidity climates), the small initial price savings becomes insignificant to the bigger financial picture over time.