EPA TO-15A Canister Leak Checking Requirements
EPA TO-15A Canister Leak Checking Requirements
By Dan Cardin
Although this article relays the requirements found in US EPA Method TO-15A, the rationale, theory, or background presented for these requirements expressed herein are based on the authors 30+ years of working with hundreds of canister laboratories world-wide, and through the inhouse research conducted at Entech Instruments, and are not necessarily found in the method and in no way represent an endorsement by the EPA. This article provides insight from a company specializing in canister sampling and analysis to help others who are endeavoring to achieve optimal performance of their methods and techniques.
TO-15A requires canisters to undergo a thorough leak check when new, and then every 3 years. The primary intention here is to test the leak “through” the isolation valve when the valve is supposed to be closed, as a leak through a faulty weld or through a poorly tightened ferrule connection at the valve/stem interface would normally not allow canisters to reach 50mtorr during cleaning. However, during normal cleaning, the valve itself is not tested to be leaktight, as the valve is open during cleaning. One way to test the valve integrity during EVERY cleaning procedure is to place all canisters on the cleaning system while the canisters are at atmospheric pressure, keeping the valves closed, and then pulling a strong vacuum on the cleaning system to try to achieve 50mtorr of high vacuum. Even a very small leak through any of the canister valves should alert the user that one or more valves are leaking because it should be difficult or impossible to reach 50mtorr of vacuum when even small leaks are present. If the vacuum system does not reach its typical high vacuum in the normal period of time (the user will quickly determine what is “normal” on their system), then often times the leaking valve can be found simply by tightening each canister valve a little more, one at a time, and watching the high vacuum readout on the cleaning system before and after tightening each valve. If the valve is marginal, just a little tightening should show a little better vacuum. A marginal valve should be either repaired or replaced. If the vacuum does not improve, move to the next canister. Likewise, each canister can be nudged left or right with a slight amount of force to see if any ferrule connections are potentially leaking. These two techniques are a great way to prove even prior to starting the cleaning process that everything is OK to start, and that the canister valves are doing their job. If you can’t get to high vacuum before opening the valves, then either there is a leak in the manifold or ferrule connections, or there is a leak through one of the valves. If you can get to high vacuum, then you’ll probably also get there after opening all valves and after the cleaning completes. This additional step can save a lab a lot of time in the long run.
Testing Canisters using Pressure
US EPA Method TO-15A allows the testing of canisters for leaks either using pressure or high vacuum. If the pressure technique is used, the canister is pressurized to 14.7 psi gauge pressure (1 atm above local atmospheric pressure, or 29.4 psi absolute pressure). The external cap can only be placed on the top of the valve loosely, not tight, just enough to keep dust out of the valve, but loose enough so the leak integrity of the valve can be evaluated. After 24 hours, the pressure is tested again, and a maximum pressure drop of 0.1 psi is allowed. Note that this pressure drop is equivalent to 41cc of gas in a 6L can, but in a 1L can this is only 41/6 = 6.8cc per day. Therefore, the EPA is looking at the potential for contamination, so the volume of allowable leakage is proportional to the size of the can, or the final dilution of the amount that has leaked into the can. Makes sense. Here is where it gets a little tricky. Since PV=nRT, a change in room temperature of just 3 deg C, say from 25C down to 22 deg C, will change the pressure in the canister from 29.4 psia to 29.4 x (295/298) = 29.1 psia. That change of 0.3 psi is 3x the amount allowable on a daily basis, so that canister will be considered a leaker, EVEN WITH ZERO LEAKAGE OUT OF THE CAN! Therefore, it is recommended to both measure the temperature of the canister carefully, and when possible, extend the test out to 7 days, where a 0.7 psi drop or less would be allowed, at which point a larger temperature swing can be tolerated. The EPA does not make any mention about an allowable adjustment of the final pressure based on canister temperature differences, so just monitor the temperature and try to make the start and end temperature as close as possible. Note that a gauge that is 0.25% accuracy is required for this test, not the standard 1.5” dial gauges typically used on canisters. A 0.25% accuracy gauge is expected to be within that accuracy across its entire range, but should have even less error at any one point in its range. That is, it should have at least a +-0.1 psi reproducibility over a several day period. Here again, allowing the canister to sit longer before testing the canister will help to eliminate any errors due to temperature swings or gauge reading inconsistencies. One more thing to note. When pressurizing a canister to 29.4 psi absolute, you are putting twice as much energy into the canister than when pressurizing the same canister to only 1 atm, or 14.7 psia. That means the canister will heat up slightly, and by as much as a few degrees. Therefore, after pressurization, allow the canister to cool down for 1 hour prior to taking the initial pressure measurement. You should soon determine what initial pressure to bring the canister up to such that the pressure will drop back down to about 29.4 psia (absolute) once it cools down.
Testing Canisters using Vacuum
TO-15A also allows canisters to be leak checked using evacuation down to 50 mtorr, and then showing that the leak rate is less than 0.1 psi per day. Considering the gas has been eliminated from the canister, there will be almost no perceivable change in pressure with a change in room temperature. Therefore, this may be the better of the two approaches. However, a different challenge arises. A gauge for measuring the absolute pressure of the canister must be found that will accurately measure 0.00 to 0.10 psi absolute. Many 0-50 or even 0-15 psi absolute gauges are not extremely accurate at 0.00 to 0.10 psia, so this must be evaluated. Some of these gauges may have a zero shift such that at 50 mtorr they will read 0.00 psia, but then even at 5200 mtorr (equivalent to 0.1 psia) they may still read 0.00 psia. The proper linear operation of the gauge should be verified down at these low pressures. As before, one solution is to wait a longer period of time, such that after 7 days, the allowable pressure rise would be up to 0.7 psia, and most gauges will read accurately down at this level. To test your gauge, place it on your canister cleaning system on an open port, and watch the pressure readings on the gauge while the vacuum increases in the cleaning system. In particular, watch for the readings when the high vacuum gauge starts to read under 2000 mtorr. The 0-15 psia gauge should read as follows:
0-15 psia Gauge 0-2000 mtorr Pirani Gauge
0.04 1999 (2000)
0.03 1500
0.02 1000
0.01 500
If the gauge reads well in this range and corresponds properly to the pirani gauge on the cleaning system, It should be able to tell the difference between 0.00 and 0.10 psia allowing a 1 day leak evaluation, although 2 days, or better 3 days over a weekend will provide a better evaluation. The EPA does not suggest a time of less than 24 hours for testing the vacuum change, but theoretically a change of 0.1 psi per day (5200 mtorr) is equivalent to 217 mtorr per hour. The challenge for testing over a shorter period would be in properly re-evacuating the volume between the top of the canister valve and the gauge once it is reconnected, as even the small volume between the top of the canister valve and the vacuum gauge may cause the canister vacuum to rise by a few hundred mtorr if the atmospheric pressure in that volume is not eliminated prior to opening the canister valve. One could perform several tests to see how much the vacuum will increase with every removal and reconnection of the high vacuum gauge when evacuation of that space is not performed prior to each re-opening of the canister, but in that case the time to wait should be long enough such that the allowable increase is many times more than the amount of increase each time the gauge is reattached and the canister valve is reopened. That is, if the pressure goes up in the canister by 300 mtorr with each removal and reattachment of the gauge, waiting 4 hours before reattaching the vacuum gauge should allow the vacuum to increase by 217 x 4 = 868 mtorr, and if the vacuum goes up by substantially less than this amount even with the 300 mtorr added by reattaching the high vacuum gauge, then this shows that the leak rate into the cans is sufficiently low. Note that this accelerated approach has not been evaluated by the EPA.
In the end, you don’t want to take the time to go through a long leak check process just to find out you have a leaking valve or ferrule connection (or leaking welds). Entech performs very fast leak check evaluation by pressurizing each canister to 40 psig (55 psia), connecting a 1/16” stainless line to the canister valve using a ¼” to 1/16” reducing ferrule, and then holding the entire canister under water using a sufficiently large tank to check for bubbles. A 0.1 psi change in a 6L can is equivalent to about 41 cc/day, or 0.028cc/min. At 40 psig, the pressure is almost 3x higher, so that would be about 0.08cc/min. A bubble coming out of the 1/16” tubing is about 0.02-0.05cc, depending on the ID of the tubing, and a few other factors, but needless to say, zero bubbles in 1-2 minutes under these conditions should ensure that your canisters will be passing the longer, BUT REQUIRED, EPA protocol listed in TO-15A.
Again, the new TO-15A should dramatically improve the quality of canister data generated, and this is very exciting to Entech. Canisters have always represented the Gold Standard in VOC air monitoring, and now the new EPA method will allow canisters to achieve their true potential. Join us next time when we discuss Time Integrated Sampling into Canisters, and the new requirements for validating cleanliness and recovery through canister sample trains.
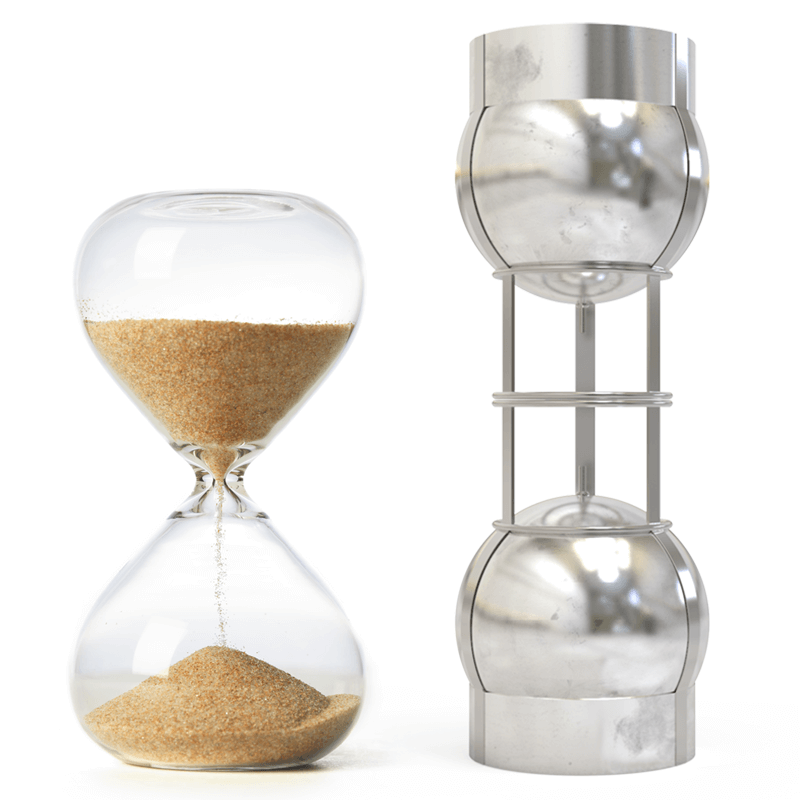
Uncoated canisters don’t save money over the life of the can.
Uncoated cans can oxidize over time and metal oxides, especially iron oxides, cause catalytic losses. When you consider the effective life of uncoated canisters, which can be much shorter than their coated counterparts (especially for those uncoated cans being utilized in high humidity climates), the small initial price savings becomes insignificant to the bigger financial picture over time.