Cleaning Canisters the Right Way!
Tricks for Getting Canisters Clean the First Time
Canister sampling and analysis remains the most effective means of monitoring C1 to C12 Volatile Organic Compounds in air. Today’s analytical systems are capable of achieving reproducibility in the range of 2-3%, which is as much as 5-10 times better than typically achieved when using thermal desorption tubes, where the tube (the preconcentration device) is changing on a per-sample basis. The only issues remaining in achieving the true potential of the canister technique is eliminating positive and negative bias resulting from inconsistencies in the canisters themselves. Negative bias is caused by using canisters that are no longer capable of maintaining compounds in the gas phase, causing them to be under-reported in the analysis. Positive bias is the result of using canisters which were not cleaned properly after the prior sampling event, leading to results that are artificially high. The condition that causes positive and negative bias are actually linked, as the same absorptive and adsorptive issues that causes negative bias losses, make canisters harder to clean up contributing to a greater potential for a positive bias, especially after collecting and storing samples with elevated levels of target compounds. Improving the inertness of canisters generally contributes to the reduction of both kinds of bias.
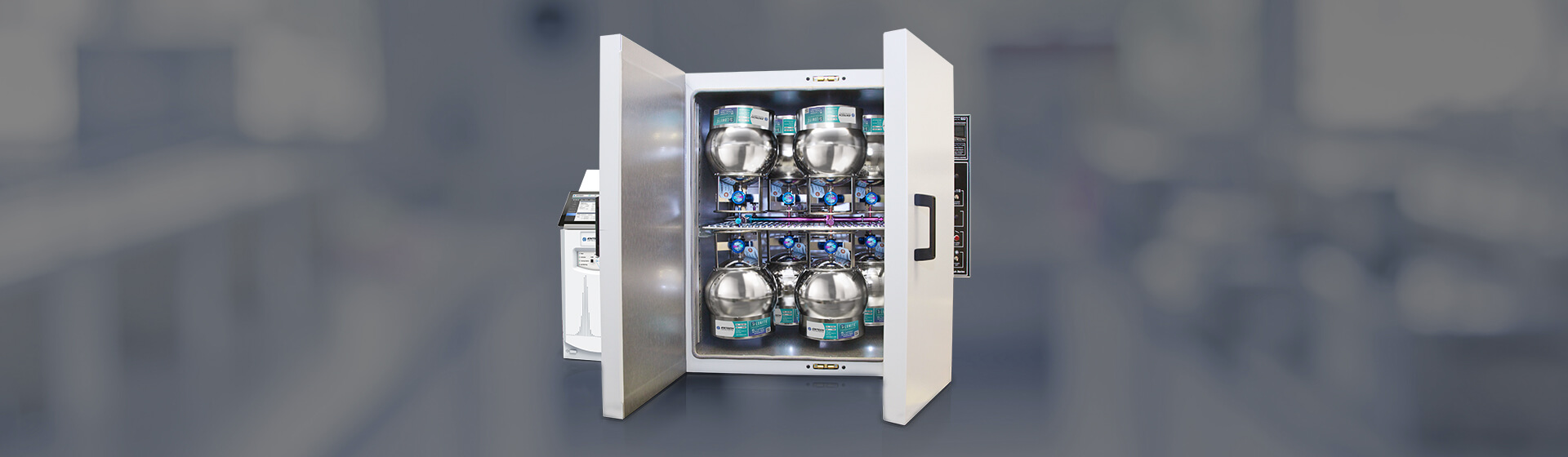
Getting canisters clean the first time is always the goal of every air lab, as the need to re-clean failed canisters adds significantly to overhead costs, while delaying the return of canisters to the field to collect the next sample. To improve the cleaning of canisters so they pass the first time, it’s important to know what is actually going on inside of the canister when samples are collected, stored, and then cleaned. EPA Method TO15 discusses the need to verify the sample train to show that it is recovering 80% of the target compounds, and the canister itself is certainly a part of that sample train. TO15 doesn’t specifically address the recovery from the canister after a reasonable holding time of, say, 2 weeks. In general, shooting for an 80% or better recovery is well within reason for this technique, again when using canisters that are inert. So, what happened to the 10-20% that are no longer in the gas phase, even with canisters that are considered to be acceptable (>80% recovery)? In most cases, the lost chemicals have not reacted, but rather have just partitioned into the walls of the canister. What’s actually happening is that chemicals will create an equilibrium concentration between the walls and the gas phase within the canister. This equilibrium will mostly set up over the first 24 hours after sampling but will continue to reach a final equilibrium over even a longer period of time. The trick to cleaning canisters is reversing this equilibrium and allowing some time for a “new equilibrium” to become established. What does this mean?
How long will it take for Compound X to come out of the walls?
Equilibrium is achieved when the rates between two states are equal. In the case of canisters, a given target compound X is going onto the walls of the canister as fast as it’s coming out. The moment canister cleaning commences and the first evacuation occurs, the equilibrium between the gas phase and the adsorbed phase in the walls has been disrupted, because the rate of transfer back into the walls drops to zero as the canister is evacuated. So how long will it take for Compound X to come out of the walls? That depends on the compound. It also depends on how much needs to come out to achieve required blank levels. Remember that if 10% of Compound X is in the canister walls, but that compound was at 1000x over the reporting limits, then there exists 100x too much of Compound X within the walls. This needs to be eliminated from the canister.
Time, temperature, and vacuum are all important to removing Compound X, and all compounds from the canister walls. With this understanding, we can see that getting canisters under vacuum ASAP after they are analyzed is critical for getting the cleanest canister. By using a separate dual stage, oil-less vacuum pump exhausted to a hood, canisters can be evacuated to just 1% of atmospheric pressure within 3-4 minutes. This will cause chemicals in the walls to start “re-equilibrating” back into the gas phase. Then, removing these canisters from the vacuum source and just allowing them to sit is actually causing them to be cleaned, as the extraction of Compound X and others is easy once they are in the gas phase. If there is an equilibrium such that 90% will be in the gas phase and only 10% in the walls, then by just sitting for a while these canisters will have 10x less in their walls compared to those canisters that were not pre-evacuated. Then, when the canisters are officially cleaned on the canister cleaner, they will be able to achieve a final cleanliness that may approach 5-10x lower than if this initial evacuation had not occurred the day before, or to a lesser yet still significant extent just several hours before. As an added benefit, the canister cleaning system will be subjected to 10x less contamination, making it easier to maintain very low background levels.
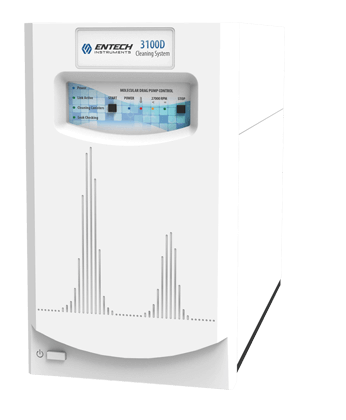
Don’t let canisters sit around with their original samples in them while they are waiting their turn to be cleaned!
Once the test results are in and the canisters can be cleaned, perform the quick, rough evacuation. Then let them sit and wait their turn. The result will be canisters that pass the first time, and a lab manager with a bigger smile on his face. And of course, when very hot samples are encountered, use this same concept but beef it up a bit. Try evacuation for a day, refill the canister, and then another quick evacuation for another day. Each time should give an attenuation of 10-50x, depending on how much has partitioned into the walls. Multiplied together, those hot cans are not going to be a problem.